To help you work through your plant installation and selection of pumps and valves we suggest using a simple
numerical scale of complexity numbered one to ten, 1 being a simple application and 10 being the most complex, for
the time being, forget about the actual pump or valve, your focus should be
your application
Your part in the process is to fill in the scale with your parameters for example in the case of dosing systems:-
No1
- we could say that the simplest application may be a hand pump in your local garage with the mechanic filling a container
with fresh oil for your car. It is manually operated, visually controlled, no repeatability is necessary and no instrumentation
is required - answer - a simple hand hand operated pump
No10 - for this application we may need a fully automated
system with status indication, fault monitoring, accurate repeatability, for aggressive or abrasive fluids installed in a
hazardous area pumping at high pressure or high flow - a complicated precision metering / dosing pump with full ATEX approval,
fully documented test data and drawings (see pages for Larox (Flowrox)Peristaltic Pumps LPP-M, LPP-D and SEKO Positive Displacement
Pumps)
These two extremes are poles apart with regard to technology and cost, your part in the process is to fill
in the parameters between 1 and 10, do not expect a No1 product to fullfil a No10 role
Selecting
valves is just as important although often overlooked as some valves are manual design, once installed they are forgotten
about until they go wrong and start costing money
The following is an example of what happens when you get things
wrong
This valve is in a pulp mill on the suction side of centrifugal pump, the media going through the valve is
extremely abrasive and is at quite high velocity. The valve was being used to control the flow from one feed into the suction
branch
The valve selected is a knife gate type, after repeated failures a high grade stainless steel valve was
installed. As you can see this also failed, the blade of the valve, the sealing ring and seat have eroded to the
point that the valve body was damaged, this valve was being changed at 6 week intervals, you can imagine the cost over a year.
The system had been causing problems for a long time
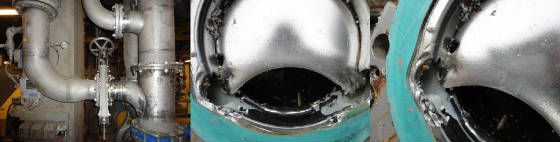
This valve has been replaced with a Larox (Flowrox)manual pinch valve sized to suit the process flows and pressures.
We anticipate the sleeve to require an annual inspection and will report on this in due course